You are just wrapping up the installation of your new antenna on your tower. You slip a bolt through the clamp and begin to tighten the nut when, suddenly, the nut freezes. It no longer turns one way or the other. What has happened is referred to as “galling” or cold welding. The only way to fix this is to either cut the bolt off or break it and start over with a new nut and bolt.
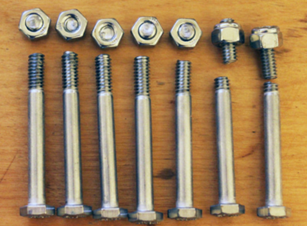
So why did this happen? Galling is defined as “a form of material wear during sliding in which macroscopic transfer of material is driven by adhesion.” Materials such as stainless steel, aluminum, titanium, and other alloys have an oxide layer on the outside surface. When a nut is screwed onto a bolt, there is friction which causes heat. Heat causes the material in the bolt to deform. Also, the oxide layer eventually gets pushed out of the way and the electrons in the metal literally fuse together, causing the bolt and nut to get stuck permanently. It isn’t that the parts melt. It’s that they get close enough together and are at a high enough energy state that they form bonds and become one part.
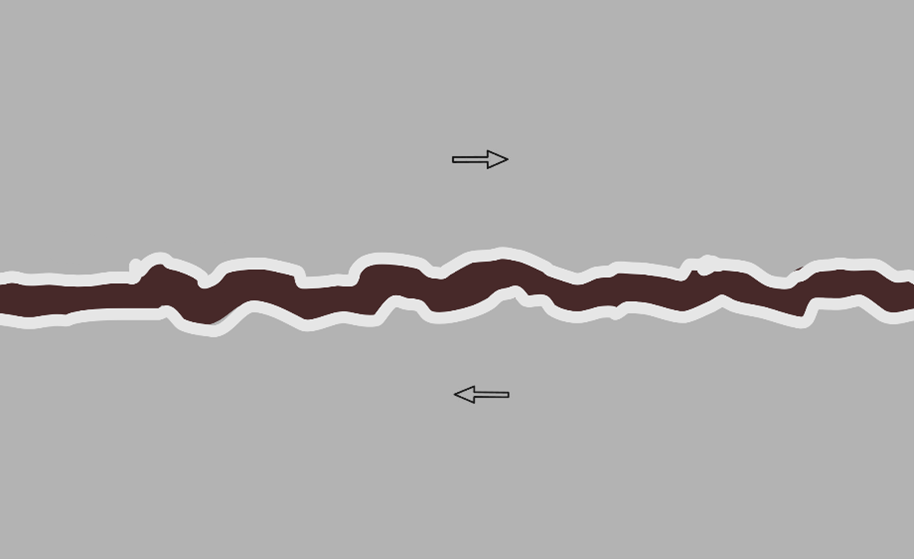
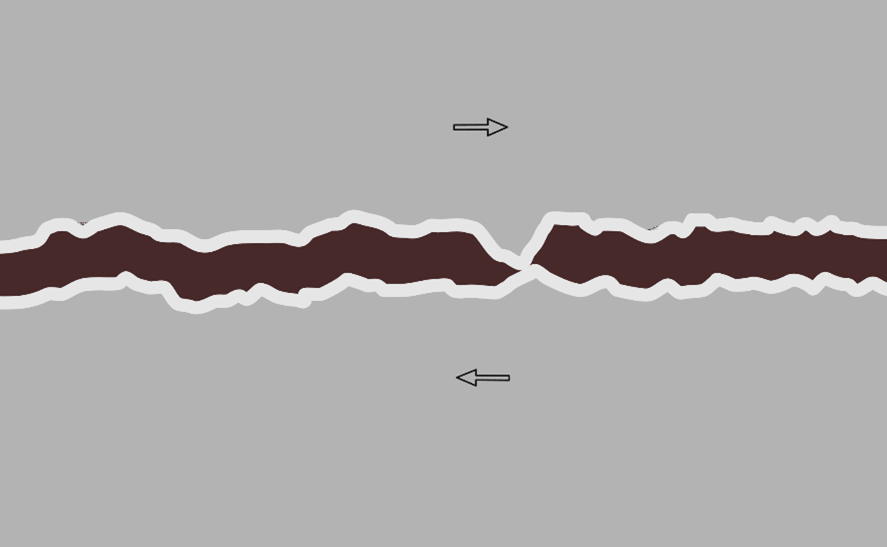
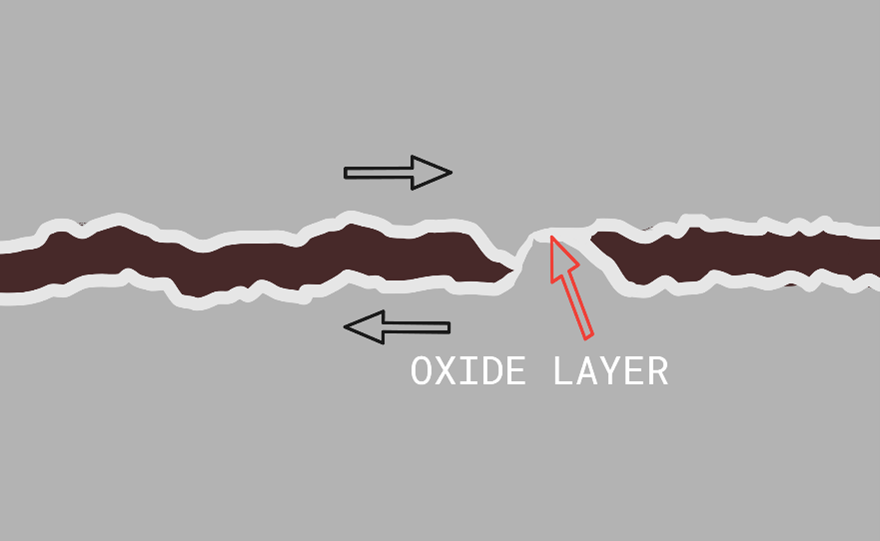
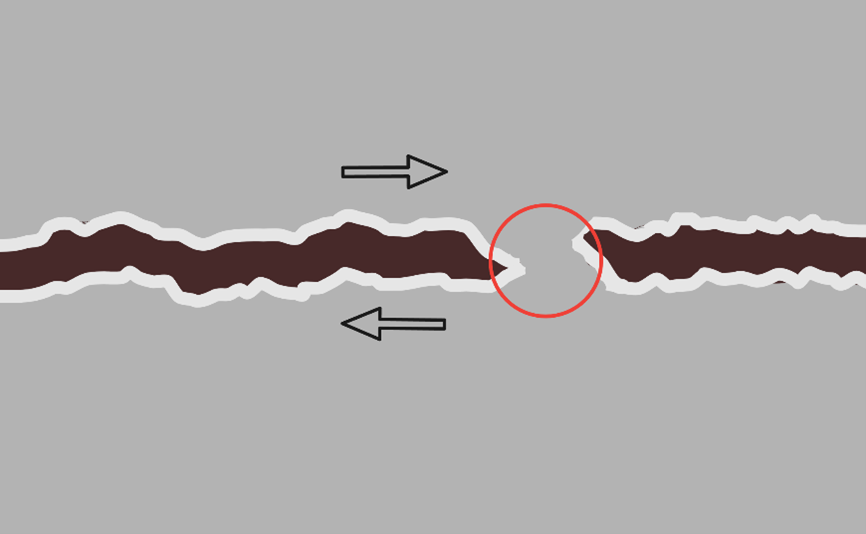
The threads on bolts and nuts appear to be smooth; however, this is not the case. Bolts are typically roll formed while nuts are mostly cut formed. So, they have two different types of threads. Rolled threads tend to be much sharper and more defined than cut threads because of the burnishing when they are manufactured.
If you look at these threads under a microscope, you will see that neither set of threads is perfect. The difference in manufacturing methods causes some resistance when the nut and bolt are threaded together.
Was something wrong with the hardware? The answer is no. What was wrong is that the customer unintentionally misused it.
Anti-Seize & Thread Lubricant
What is the best way to keep this from happening? The best solution is to apply a lubricant to the threads such as Jet-Lube SS-30 Pure Copper Anti-Seize. Contest stations, including K3LR and W3LPL, use Jet-Lube SS-30 as their choice for antenna assembly and on all of their hardware. This PDF shows some K3LR antenna installations that relied on Jet-Lube SS-30.
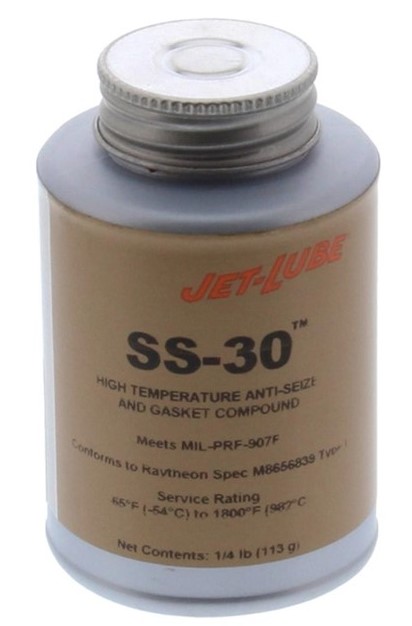
Other Anti-Seize Options
Permatex Anti-Seize
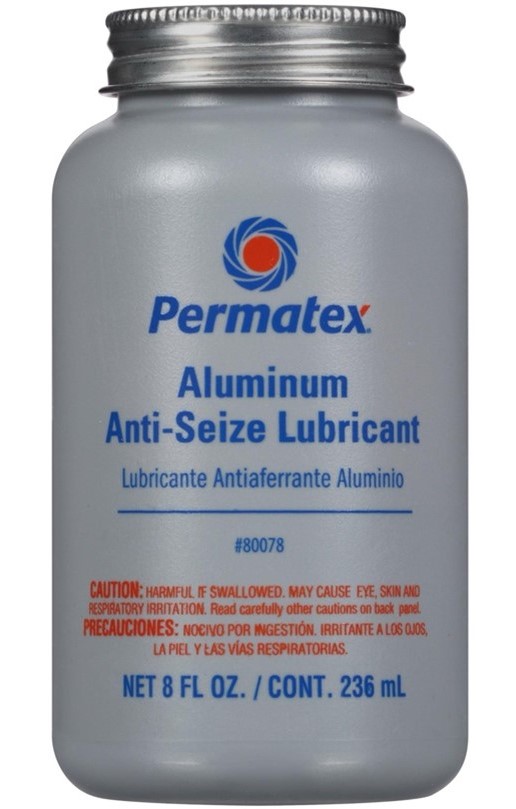
Never-Seez
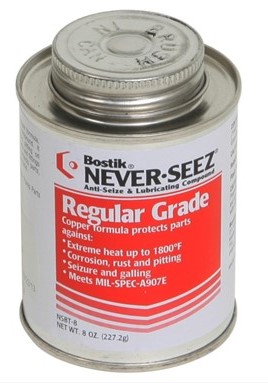
Adding a small amount of lubricant creates a barrier which reduces friction and will reduce or eliminate galling.
Galling is an all-too-common occurrence that can easily be mitigated. By using the proper lubricant and not over-torquing, you can avoid the frustration of having to cut or break a bolt. And no one wants to do that at 100 feet in the air. (Ask me how I know.)
Read this article available at DXEngineering.com for more details on galling and recommended thread lubricants.
Also, watch this DX Engineering video for further information: